Acrylnitril-Butadien-Styrol-Copolymer
Strukturformel | |||||||
---|---|---|---|---|---|---|---|
![]() | |||||||
Typischer Ausschnitt aus dem ABS Pfropfcopolymer[1] | |||||||
Allgemeines | |||||||
Name | Acrylnitril-Butadien-Styrol | ||||||
Andere Namen |
| ||||||
CAS-Nummer | 9003-56-9 | ||||||
Monomere/Teilstrukturen | Acrylnitril, Butadien und Styrol | ||||||
Art des Polymers |
Copolymer | ||||||
Eigenschaften | |||||||
Aggregatzustand |
fest | ||||||
Härte |
70–80 Shore-D-Härte[2] | ||||||
Löslichkeit |
| ||||||
Sicherheitshinweise | |||||||
| |||||||
Soweit möglich und gebräuchlich, werden SI-Einheiten verwendet. Wenn nicht anders vermerkt, gelten die angegebenen Daten bei Standardbedingungen. |

Acrylnitril-Butadien-Styrol-Copolymere (Kurzzeichen ABS) sind thermoplastische Terpolymere, bei denen an eine Polybutadien-basierte Hauptkette kovalent Seitenketten aus Styrol-Acrylnitril-Copolymer (SAN) angebunden sind. Da die beiden Komponenten nicht ineinander löslich sind, tritt eine Mikrophasenseparation auf, die durch die eingelagerten, weichen Polybutadienpartikel in der kontinuierlichen, spröden SAN-Hauptphase die Schlagzähigkeit des Materials erhöht. Die Mengenverhältnisse der eingesetzten Monomere variieren im Bereich von 5 bis 30 % Butadien sowie 15–35 % Acrylnitril und 40–60 % Styrol.
Kunststoffe mit ähnlicher Zusammensetzung sind Styrol-Butadien-Styrol (nur aus Styrol und Butadien), Nitrilkautschuk (nur Acrylnitril und Butadien) und Styrol-Acrylnitril-Copolymer (SAN, nur Styrol und Acrylnitril).
ABS-Kunststoffe
[Bearbeiten | Quelltext bearbeiten]Die ISO-Norm ISO 472:2013 (de) bezeichnet Acrylnitril-Butadien-Styrol-Kunststoff als Kunststoff aus Terpolymeren und/oder Mischungen von aus Acrylnitril, Butadien und Styrol hergestellten Polymeren und Copolymeren.[5]
Als technischer Kunststoff besteht ABS sehr häufig aus einem Blend des Terpolymers mit der reinen Hartkomponente SAN, da hierdurch bei gleichem Hart-/Weichphasenanteil und gleichem Molgewicht der PB-Weichphase das mittlere Molgewicht deutlich verringert und damit die Verarbeitbarkeit verbessert wird. Das Material besteht dann aus einem PB-Kern und der ineinander gelösten graft-Schale und SAN-Matrix.[6]
Auch Varianten, in denen anstatt einer reinen PB-Hauptkette Nitrilkautschuk (Poly-(butadien-stat-acrylnitril)) oder SBR (Poly-(styrol-co-butadien)) eingesetzt wird, sind bekannt. Die (partielle) Verwendung von Methylstyrol statt Styrol erhöht die Temperaturbeständigkeit des Materials (höherer Glaspunkt der (M)SAN-Phase), ebenso die Copolymerisation von Styrol mit Maleinsäureanhydrid. Durchsichtige Varianten werden erhalten, wenn der Brechungsindex der Hartphase durch Copolymerisation mit Methylmethacrylat an den der PB-Weichphase angeglichen wird. Für bessere Umweltstabilität kann das UV- und Ozon-empfindliche PB durch EPDM ersetzt werden.[6]
Herstellung
[Bearbeiten | Quelltext bearbeiten]ABS wird großtechnisch durch Pfropfcopolymerisation hergestellt.[7] Hier unterscheidet man das Emulsions- und das Masse-Verfahren:
- Emulsionsverfahren
- Polybutadien wird durch Emulsionspolymerisation hergestellt und mit den anderen Monomeren (Mischung aus Styrol und Acrylnitril) gepfropft. Das Produkt wird getrocknet und in der Wärme mit separat hergestelltem Poly(styrol-co-Acrylnitril) vermischt. Da bei der Emulsionspolymerisation typischerweise hohe Molekulargewichte vorliegen, sind die Weichphasen des bei diesem Verfahren gebildeten Polymers besonders groß (Durchmesser von 300 bis 600 nm).[8]
- Masse-Verfahren
- Auch hier liegt bereits Polybutadien vor, welches in einer Reaktionslösung mit Acrylnitril- und Styrolmonomeren gelöst wird. Diese Reaktionslösung wird dann auf „graft-from“-Art zum Pfropfcopolymer polymerisiert. Es handelt sich um eine Substanzpolymerisation. Das Produkt dieser Polymerisation ist allerdings kein „reines“ Pfropfcopolymer, sondern es entsteht ein Blendpolymer. Dies liegt daran, dass sich Polybutadien nicht im bei der Polymerisation entstehenden Poly(styrol-co-acrylnitril) löst, sondern nur in der Monomerenmischung. Restliches Polybutadien fällt daher nicht aus, sondern wird in das Produkt der Polymerisation eingelagert. Man spricht von einer Weichphase, bei der Polybutadien in eine Styrol-Acrylnitril-Matrix eingebettet ist. Typische Durchmesser des eingelagerten gepfropften Polybutadiens sind 1–4 µm.[9]
Eigenschaften
[Bearbeiten | Quelltext bearbeiten]ABS ist in Rohform ein farbloser bis grauer Feststoff. Es kann mit Methylethylketon (MEK) und Dichlormethan (Methylenchlorid) geklebt werden.
Weitere Eigenschaften sind:
- Dichte: 1,04 g/cm³
- Reißdehnung (DIN 53455): 15 bis 30 %
- linearer Ausdehnungskoeffizient: 60–110 K−1 · 10−6
- spez. Wärmekapazität: 1,3 kJ · kg−1 · K−1
- Dauergebrauchstemperatur: max. 85 bis 100 °C
- elektrische Durchschlagsfestigkeit bis zu 120 kV · mm−1
- Beständigkeit gegen Öle und Fette
- temperaturbeständig
- Beständigkeit gegen Witterungseinflüsse und Alterung[10]
Verwendung
[Bearbeiten | Quelltext bearbeiten]
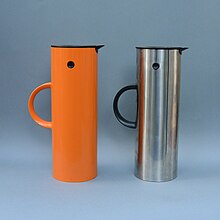

Haushalts- und Konsumprodukte dominieren die weltweite Nachfrage nach Acrylnitril-Butadien-Styrol.[11] Deutlich mehr als 50 % der ABS-Produktion in Westeuropa wird von der Automobil- und Elektroindustrie verwendet. ABS eignet sich gut zum Beschichten mit Metallen (Galvanisieren) und Polymeren. Dies macht es zum Beispiel möglich, eine verchromte Oberfläche auf einem Kunststoffteil zu erhalten. Beispiele für den Einsatz von ABS sind thermogeformte Teile aus Platten und Folien, Automobil- und Elektronikteile, Motorradhelme, Spielzeug (zum Beispiel Lego-Bausteine oder Playmobil-Figuren[12]), Gehäuse von Elektrogeräten und Computern,[13] Kantenbänder (Umleimer) in der Möbelindustrie, Konsumgüter mit erhöhten Ansprüchen an die Schlagzähigkeit, Musikinstrumente (zum Beispiel Klarinetten- und Saxophon-Mundstücke, Ukulelen-Korpusse oder Randeinfassungen von Gitarren) und die Seitenwangen von in Sandwichbauweise hergestellten Skiern und Snowboards. ABS wird auch als Filament für das 3D-Druckverfahren Fused Deposition Modeling verwendet und eignet sich durch die hohe Stabilität und vielfältige Nachbearbeitungsmöglichkeiten (schleifen, lackieren, kleben, fillern) insbesondere für die Produktion von Prototypen. Besondere Formen von ABS-Filamenten sind ABS-ESD (electrostatic discharge) und ABS-FR (fire resistant), die insbesondere für die Produktion elektrostatisch gefährdeter Bauelemente und feuerfester Fertigteile verwendet werden.[14]
Verarbeitung
[Bearbeiten | Quelltext bearbeiten]Standard-ABS erweichen um 95–110 °C (siehe Vicat-Erweichungstemperatur). Typische Verarbeitungstemperaturen beim Spritzgussverfahren oder allgemein per Extrusion liegen im Bereich von 220–250 °C (Hochtemperatur-ABS-Blends noch höher). Als eine spezielle Form letzterer Methode ist ABS auch ein üblicher Werkstoff für 3D-Drucker.
Es eignet sich nach Vorbehandlung hervorragend zum Galvanisieren, Lackieren und Bedrucken. Warmgas-, Heizelement-, Rotationsreibschweißen sowie Ultraschall- und Hochfrequenzschweißen sind möglich.[10]
Recycling
[Bearbeiten | Quelltext bearbeiten]
Bei sauberer Trennung kann ABS problemlos wieder eingeschmolzen und wiederverwendet werden. Zur Sortierung stehen maschinelle Verfahren zur Verfügung, die es aus üblichen Abfallmischungen zu einem Reinheitsgrad von über 99 % separieren können.[15]
Normen
[Bearbeiten | Quelltext bearbeiten]- DIN EN ISO 2580-1 Kunststoffe – Acrylnitril-Butadien-Styrol (ABS)-Formmassen – Teil 1: Bezeichnungssystem und Basis für Spezifikationen (ISO 2580-1:2002). Deutsche Fassung EN ISO 2580-1:2002.
- DIN EN ISO 2580-2 Kunststoffe – Acrylnitril-Butadien-Styrol (ABS)-Formmassen – Teil 2: Herstellung von Probekörpern und Bestimmung von Eigenschaften (ISO 2580-2:2003). Deutsche Fassung EN ISO 2580-2:2003.
Handelsnamen
[Bearbeiten | Quelltext bearbeiten]
|
|
Quellen
[Bearbeiten | Quelltext bearbeiten]- ↑ Wolfgang Kaiser: Kunststoffchemie für Ingenieure: von der Synthese bis zur Anwendung, 3. Aufl., Hanser-Verlag, München 2011, S. 311, ISBN 978-3-446-43049-5.
- ↑ Shore-Härte bei polymerservice-merseburg.de
- ↑ a b Datenblatt ABS ( vom 27. Februar 2012 im Internet Archive) bei unicgroup.com (PDF; 157 kB), abgerufen am 11. Juni 2013.
- ↑ a b Datenblatt Poly(acrylonitrile-co-butadiene-co-styrene), acrylonitrile ~40 wt. %, powder bei Sigma-Aldrich, abgerufen am 27. Dezember 2012 (PDF).
- ↑ ISO-Norm ISO 472:2013 (de)
- ↑ a b Andreas Chrisochoou and Daniel Dufour, Styrenic Copolymers, Rapra Review Reports Vol. 13, 11, ISBN 1-85957-363-0 [1]
- ↑ Karlheinz Biederbick: Kunststoffe, 4. Auflage, Vogel-Verlag, Würzburg, 1977, S. 87, ISBN 3-8023-0010-6.
- ↑ Sebastian Koltzenburg, Michael Maskos, Oskar Nuyken: Polymere: Synthese, Eigenschaften und Anwendungen. 1. Auflage. Springer Spektrum, Heidelberg 2014, ISBN 978-3-642-34772-6, S. 416.
- ↑ Sebastian Koltzenburg, Michael Maskos, Oskar Nuyken: Polymere: Synthese, Eigenschaften und Anwendungen. 1. Auflage. Springer Spektrum, Heidelberg 2014, ISBN 978-3-642-34772-6, S. 415.
- ↑ a b Christian Bonten: Kunststofftechnik Einführung und Grundlagen, Hanser Verlag, 2014.
- ↑ Marktstudie Technische Kunststoffe, Ceresana, Sep. 2013.
- ↑ Jochen Bettzieche: Playmobil ohne Erdöl. In: nzz.ch. 17. Juli 2012, abgerufen am 14. Januar 2019.
- ↑ Anirban Saha: ABS vs PBT keycaps. Abgerufen am 22. Juli 2021 (englisch).
- ↑ 3D-Druck: Aktuelle Anwendungsbeispiele. 15. Februar 2016, abgerufen am 30. April 2019.
- ↑ Argonne National Laboratory: Process for Recovering Usable Plastics from Mixed Plastic Waste ( vom 15. März 2012 im Internet Archive).