Fördermaschine

Eine Fördermaschine,[1] auch Schachtfördermaschine genannt,[2] ist eine maschinelle Einrichtung, die im Bergbau zum Antrieb der Förderkörbe oder -gefäße dient.[1] Sie wird als Antrieb in Schacht- und Schrägförderanlagen eingesetzt.[3]
Die Fördermaschine ist auf einem Bergwerk eine der wichtigsten Maschinen.[2] Ihre Leistung ist bei modernen Fördermaschinen erheblich höher als die der anderen Förderantriebe des Bergwerks.[4] Denn nur mit einer ausreichend leistungsfähigen Schachtfördermaschine ist die Förderung von Material und Produkten sowie die Beförderung von Bergleuten aus großen Teufen möglich.[5]
Geschichte
[Bearbeiten | Quelltext bearbeiten]
Die Urform der Fördermaschine ist der Handhaspel, nach heutiger Klassifikation eine über dem Schacht aufgestellte muskelkraftbetriebene Ein-Trommel-Maschine.[3] Als der Bergbau in größere Teufen vordrang, wurde mehr Antriebsenergie benötigt und dies führte zur Konstruktion und Einsatz von Treträdern, Pferdegöpeln und Kehrrädern.[6] Nunmehr ging man von der Aufstellung über dem Schacht ab und positionierte diese frühen Fördermaschinen seitlich davon.[7] Teilweise wurden Kehrräder auch untertägig in Radstuben installiert, wobei das Aufschlagwasser über Aufschlageröschen zu- und über Ablaufröschen abgeführt wurde.[6] Bei dieser im Erzbergbau vom Mittelalter bis zum Beginn der Industrialisierung gebräuchlichen Anordnung wurden die Förderseile entweder durch separate Seilkanäle oder durch den Schacht selbst bis nach über Tage in das Treibehaus geführt und durch Seilscheiben wieder in den Schacht hinein umgelenkt.[8] Durch die Anordnung der Leitschaufeln in zwei Kränzen mit entgegengesetzter Ausrichtung konnten die Seilkörbe in beide Richtungen angetrieben werden.[9]
Der Begriff der Fördermaschine bildete sich mit der Einführung der Dampfmaschine für die Schachtförderung heraus.[10] Mit dem Einsatz der Dampfmaschinen wurde der Übergang zum Tiefbau eingeleitet.[11] Bis zum Beginn des 20. Jahrhunderts wurden die Fördermaschinen ausschließlich mit Dampf angetrieben.[2] Durch die fortschreitende Elektrifizierung der Bergwerke, wurden allmählich auch elektrische Fördermaschinen auf den Bergwerken eingesetzt.[12] Die Verwendung dieser Maschinen war ein Wendepunkt in der Entwicklung der Fördermaschinentechnik.[2] Die ersten elektrischen Fördermaschinen wurden Anfang des 20. Jahrhunderts auf den von Arnim’schen Steinkohlenwerken in Planitz bei Zwickau (Neuer Heinrichschacht 1899 bzw. Neuer Alexanderschacht 1902) aufgestellt.[10] Lange Zeit wurden danach sowohl elektrische als auch dampfbetriebene Fördermaschinen eingesetzt.[2] Welcher von beiden Antrieben letztendlich eingebaut wurde, hatte sowohl wirtschaftliche als auch betriebstechnische Gründe.[13]
Im Laufe der Jahre wurden immer leistungsstärkere Fördermaschinenantriebe gebaut, sodass bereits im Jahr 1914 die erste elektrische Fördermaschine mit zwei parallel geschalteten Elektromotoren mit einer Leistung von 1500 Kilowatt in Betrieb genommen werden konnte.[14] Zudem wies die Dampfmaschine gegenüber der elektrischen Fördermaschine erhebliche Nachteile auf, was die Steuerbarkeit und Wirtschaftlichkeit betraf.[15] Insbesondere bei den Bremsvorgängen, bei denen in vielen Fällen Gegendampf verwendet werden musste, wurde ihre Effizienz stark gemindert.[16] Außerdem hatte die Dampffördermaschine einen schlechteren Wirkungsgrad bei der Energieumwandlung als die elektrische Fördermaschine.[17] Bedingt ihrer schlechten Steuerbarkeit durfte die Dampffördermaschine aufgrund bergbehördlicher Anordnung bei der Seilfahrt nur mit einer Fahrgeschwindigkeit von sechs Metern pro Sekunde gefahren werden.[14] Letztendlich ließ sie sich nicht automatisieren.[17] Bedingt durch die vielen Nachteile geriet die Dampffördermaschine gegenüber der elektrischen Fördermaschine stark ins Hintertreffen.[14] Dies führte dazu, dass die Dampffördermaschine von der elektrischen Fördermaschine weitestgehend verdrängt wurde.[17] Dennoch wurden vereinzelt auch weiterhin Dampffördermaschinen für die Schachtförderung eingesetzt, wie z. B. auf der Zeche Fürst Leopold Wulfen, auf der bis etwa zum Jahr 2008 eine Dampffördermaschine in Betrieb war.[18]
Aufbau
[Bearbeiten | Quelltext bearbeiten]Eine Fördermaschine besteht im Wesentlichen aus den folgenden 5 Komponenten:
- Seilträger
- Antrieb (Antriebsmaschine und gegebenenfalls Getriebe)
- Bremseinrichtungen
- Steuer- und Regeleinrichtungen
- Bedienstände
Ebenfalls dazu gehören die erforderlichen Verlagerungen und Fundamente.[19]
Seilträger
[Bearbeiten | Quelltext bearbeiten]Der Begriff Seilträger entstand aus der Notwendigkeit heraus, einen gemeinsamen Oberbegriff für die Seilkörbe, -trommeln, Treibscheiben oder Bobinen zu finden. Der Seilträger nimmt das Förderseil auf, das mit dem im Schacht befindlichen Fördermittel bzw. Förderkorb verbunden ist.[20] Durch Drehung des Seilträgers wird über das Förderseil das im Schacht befindliche Fördermittel in Auf- oder in Abwärtsrichtung bewegt.[21] Es gibt insgesamt drei verschiedene Arten von Seilträgern, Treibscheibe, Trommel und Bobine.[22] Trommeln werden als Seilträger verwendet, wenn aus besonders tiefen Schächten gefördert wird.[23] Treibscheiben (auch Koepescheiben genannt) können als Seilträger sowohl bei Flurfördermaschinen als auch bei Turmmaschinen verwendet werden.[24] Die Bobine wird als Seilträger für Fördermaschinen genutzt, die zum Schachtteufen eingesetzt werden.[25] Als Förderseile werden Flachseile verwendet.[22]
Antrieb
[Bearbeiten | Quelltext bearbeiten]Der Antrieb besteht hauptsächlich aus der Antriebsmaschine.[4] Bei einigen bestimmten Fördermaschinen wird zwischen Antriebsmaschine und Seilträger ein Getriebe geschaltet.[16] Dies ist immer dann erforderlich, wenn die Drehzahl des Antriebsmaschine zu hoch ist und sich nicht genügend runterregeln lässt.[19] Entsprechend ihrer Antriebsenergie wurden als Antriebsmaschinen Wasserkraftmaschinen,[2] Dampfmaschinen, Druckluftmaschinen[3] oder Elektromotoren verwendet.[2] Da die Fördermaschine die Energie, die sie benötigt, nur unregelmäßig abnimmt, müssen zusätzliche Einrichtungen wie z. B. Speicher installiert sein, damit die Energieversorgung durch Kraftwerk, Kesselhaus oder elektrische Zentrale nicht ungünstig beeinflusst wird.[26]
Wasserkraftmaschinen
[Bearbeiten | Quelltext bearbeiten]Bei den mittels Wasserkraft angetriebenen Fördermaschinen wurden überwiegend oberschlächtige Wasserräder verwendet.[27] Diese Kehrräder sind durch einen mittleren Kranz in zwei Hälften geteilt.[8] An dem mittleren Kranz greift auch die Bremse an.[27] Diese Kehrräder hatten einen Durchmesser von bis zu zwölf Metern und eine Breite von etwa zwei Metern[ANM 1] und wurden je nach örtlicher Gegebenheit entweder über Tage oder unter Tage eingebaut.[9] Die Seilkörbe sind auf der verlängerten Wasserradwelle montiert.[8] Teilweise wurden auch Turbinen als Antriebsmaschinen verwendet.[3] Da diese Maschinen eine höhere Drehzahl haben, werden sie über ein Vorgelege mit der Seilkorbwelle verbunden.[28] Aufgrund der erforderlichen Fallenergie werden die Wasserkraftmaschinen in der Regel Untertage im Schacht so eingebaut, dass das Aufschlagwasser über den tiefsten Stollen abgeleitet werden kann.[27] Die Schütze für die Wasserradsteuerung werden ebenfalls Untertage eingebaut und sind über Gestänge mit dem übertägigen Bedienstand verbunden.[8] Die Seile werden zu den übertägigen Seilscheiben gelenkt.[29]
Dampfmaschinen
[Bearbeiten | Quelltext bearbeiten]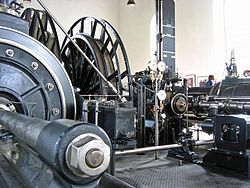
Die ersten im Bergbau betriebenen Dampfmaschinen wurden für die Wasserhaltung der Grubengebäude eingesetzt.[14] Im englischen Bergbau wurde im Jahr 1776 die erste von James Watt konstruierte Dampfmaschine auf einem Bergwerk eingesetzt.[30] Die ersten als Fördermaschine eingesetzten Dampfmaschinen wurden im Ruhrbergbau bereits zu Anfang des 19. Jahrhunderts auf der Zeche Wohlgemut eingebaut.[11] Diese ersten Maschinen verfügten über eine Leistung von nur wenigen PS.[31] Mit diesen Fördermaschinen war man in der Lage, eine Nutzlast von einer Tonne aus einer Teufe von 150 Metern mit einer Geschwindigkeit von 2 Meter pro Sekunde zu fördern. Als Seilträger wurden wegen der starken Vibrationen Bobinen verwendet.[32] Modernere Maschinen hatten schon bald Leistungen von bis zu 70 PS und mehr.[33] Sie arbeiteten mit einem Dampfdruck von 3 bis 5 Atmosphären.[32] Der Druck konnte ungehindert aus den Auslassventilen entweichen, da an den Maschinen in der Regel kein Expansionsapparat installiert war.[30] Die Expansionsapparate wurden nicht angebracht, da sie sich bei der Umsteuerung als nachteilig erwiesen hatte.[33] Nachteilig waren bei diesen Maschinen die großen Dimensionen der Schieber und die aufgrund der Größe damit verbundene manuelle Beweglichkeit der Schieber.[34] Einige der Maschinen hatten oft eine Doppelfunktion, sie wurden gleichzeitig als Fördermaschine und zur Wasserhaltung eingesetzt.[32]
Im Laufe der Jahre wurden immer leistungsfähigere Maschinen gebaut und auf den Bergwerken eingesetzt.[16] Bis etwa zur Jahrhundertwende vom 19. ins 20. Jahrhundert waren die Zwillingsdampffördermaschinen mit direktem Antrieb die vorherrschenden Antriebsmaschinen.[13] Diese Maschinen waren für eine Dampfspannung von mehr als acht Atü geeignet.[26] Die Maschinen waren anfänglich mit einer Kulissensteuerung ausgestattet.[35] Später wurde anstelle der Kulissensteuerung die Knaggensteuerung verwendet.[13] Bei dieser Steuerungsart werden die Ventile der Dampfmaschine durch unrunde Körper, die man als Knaggen bezeichnet, angetrieben.[35] Zu Beginn des 20. Jahrhunderts kamen anstelle der Zwillingsmaschinen die Verbundmaschinen als Antriebsmaschinen zum Einsatz.[16]
Zur Dampfversorgung musste jede Schachtanlage ein Kesselhaus haben.[36][16] Als Dampfkessel kamen ursprünglich Flammrohrkessel zum Einsatz, oft in der Ausführung eines Doppelflammrohrkessels, die mit Drücken von 10 bis 16 bar betrieben wurden.[36] Meistens wurde noch ein so genannter Ruthsspeicher zwischen Dampferzeuger und Dampfmaschine zwischengeschaltet.[37] Diese Speicher haben ein Volumen von mehreren 10.000 l und sind mit Heißwasser im Siedezustand gefüllt.[36] Der Dampf aus dem Dampfkessel wird durch Düsenrohre im unteren Bereich der Speicher eingeleitet.[38] Da die Dampfmaschine beim Anlaufen mit hoher Überlast betrieben wird, können durch die Nachverdampfung aus der großen Wassermenge in dem Ruthsspeicher kurzzeitig erhebliche Dampfmengen zur Verfügung gestellt werden.[35] Vom Kesselhaus wurde der Dampf über Rohrleitungen zu den Fördermaschinen geleitet.[39]
- Beispiele von Dampffördermaschinen

Die 12 PS starke Dampfmaschine des 125 m tiefen St.-Lampertus-Richtschachtes wurde seit 1876 zum Antrieb der gusseisernen Pumpensätze und seit 1880 auch zum Antrieb der Fördermaschine genutzt.[40]
Auf der Zeche Fürst Leopold in Dorsten (zuletzt Teil des 2008 stillgelegten Bergwerks Lippe) stand die letzte im Ruhrbergbau betriebene Zwillingsdampfmaschine an Schacht 2. Die Maschine wurde Mitte 2008 stillgelegt.[41]
Auf dem Bergwerk Ibbenbüren befindet sich am Schacht von Oeynhausen 1 eine Dampffördermaschine in der heute seltenen Bauform einer Doppel-Trommelfördermaschine. Teilweise ist an zurückgebauten Förderanlagen mit Dampfmaschinen der Antrieb auf Druckluft umgerüstet worden (z. B. Malakowturm Schacht 1 der Zeche Ewald).
Auf dem Bergwerk Auguste Victoria in Marl sind bis 2007 noch insgesamt drei ehemalige Dampffördermaschinen im Einsatz gewesen. 1966 wurden diese Maschinen auf Niederdruck umgerüstet. Die Maschinen sind aus den Jahren 1904 und 1907 (GHH Sterkrade) und 1911 (Isselburg). Die Schächte wurden zwischenzeitlich stillgelegt und verfüllt.
Auf dem Industriedenkmal Zeche Consolidation Schacht 9 in Gelsenkirchen[42] steht die 1963 von der Gutehoffnungshütte gebaute größte Dampffördermaschine Europas. Die zweizylindrige Zwillingsdampfmaschine hat eine Leistung von 4100 PS, wiegt 285 Tonnen und hob Nutzlasten von 12 Tonnen mit einer Geschwindigkeit von 18 m/s aus dem 1000 m tiefen Schacht. Die Maschine wird an jedem 1. Sonntag im Monat im Museumsbetrieb vorgeführt und läuft dabei wie im regulären Betrieb auf Druckluft.[43]
Druckluftmaschinen
[Bearbeiten | Quelltext bearbeiten]Als Druckluftmaschinen wurden im Bergbau Einzylindermaschinen und Zwillingsmaschinen eingesetzt.[2] Die Maschinen arbeiten bei einem Überdruck von 3 bis 5 Bar. Die Druckluftzufuhr für die Maschinen wurde vom Maschinenwärter über ein Absperrventil geregelt. Die Maschinen wurden hauptsächlich als Blindschachtmaschine oder als Teufhaspel verwendet.[4] Die Maschinen ähneln von ihrem prinzipiellen Aufbau dem Aufbau der Dampfmaschinen.[2] Da Druckluftmaschinen mit Luft als Antriebsmedium arbeiten und diese Luft eine höhere Dichte hat als Dampf, sind die Ein- und Ausströmöffnungen beim Schieberkasten und beim Zylinder etwas größer als bei der Dampfmaschine. Einzylindrische Maschinen werden mit einem Schwungrad betrieben, dieses ist beim Zwillingshaspel nicht erforderlich. Zwillingsmaschinen wurden oftmals in Doppelfunktion auch zur Wasserhaltung verwendet. Druckluftmaschinen wurden im westfälischen Steinkohlenbergbau und im Saarbergbau eingesetzt.[3]
Fördermaschine mit Elektromotor
[Bearbeiten | Quelltext bearbeiten]
Bis zu Beginn des 20. Jahrhunderts wurden Elektromotoren nur vereinzelt und auch nur für den Antrieb kleiner Fördermaschinen verwendet.[44] Dies lag in erster Linie daran, dass an Fördermaschinen, die an Schächten eingesetzt wurden und an denen auch Seilfahrt stattfand, höhere Anforderungen bezüglich ihrer Manövrierfähigkeit gestellt wurden.[45] In der ersten Hälfte des 20. Jahrhunderts setzten die Bergwerksbetreiber verstärkt auf elektrische Fördermaschinenantriebe.[16] Dies lag daran, dass bei neu errichten Förderstandorten, aufgrund von Erweiterungen der Grubenfelder, auf den Bau von neuen Dampfkesselanlagen verzichtet wurde und lieber auf die elektrischen Antriebe gesetzt wurde.[45] Als Antriebsmotoren für die Fördermaschine wurden / werden sowohl Gleichstrom- als auch Drehstrommotoren verwendet.[36] Um die Ausfallrate zu reduzieren, werden häufig zwei gleichstarke und gleichartige Elektromotoren zum Antrieb des Seilträgers verwendet.[16] Moderne Fördermaschinen werden heute fast ausschließlich mit Elektromotor angetrieben.[23] Ein wesentlicher Vorteil der elektrischen Fördermaschinen ist, dass sie automatisierbar sind.[17] Außerdem haben Elektromotoren ein gleichförmiges Drehmoment, was sich wiederum positiv auf die Lebensdauer und somit auch auf die Aufliegezeit der Förderseile auswirkt.[13]
Fördermaschinen mit Gleichstrommotor
[Bearbeiten | Quelltext bearbeiten]Die Anforderungen an Fördermaschinen, hohes Drehmoment bei gleichzeitig geringer Drehzahl sowie stufenlose Regelung der Geschwindigkeit, konnten zunächst nur Gleichstrommaschinen erfüllen.[44] Bei diesen Antrieben werden fremderregte Gleichstrommotoren mit Drehzahlstellung über die Feld- oder die Ankerwicklung verwendet.[36] Die Stromversorgung mit Gleichstrom erfolgte bei Antrieben kleiner und mittlerer Leistung über einen separaten Gleichstromgenerator.[12] Zum Ausgleich von Belastungsschwankungen war eine Pufferbatterie parallel zugeschaltet, die so dimensioniert war, dass sie bei Ausfall des Generators genügend elektrische Energie lieferte, um das Fördertreiben bis zum Endpunkt zu beenden.[45] Bei größeren Maschinen setzt man auf eine andere Art der Stromversorgung mit Gleichstrom für die Fördermaschinenmotoren.[36] Zur Versorgung mit dem erforderlichen Gleichstrom verwendet man den sogenannten Ilgner-Umformer,[ANM 2] der mit einer mehrere Tonnen schweren Schwungscheibe zum Ausgleich für Stoßbelastungen ausgestattet war.[46] Später wurden dann Leonardumformer für die Stromversorgung der Fördermaschinen verwendet.[47] Dort, wo es die Verhältnisse des Stromnetzes zuließen, wurden zur Erzeugung des Gleichstromes auch Quecksilberdampfgleichrichter eingesetzt.[17] Sowohl die Stromrichtung als auch die Höhe der Gleichspannung und damit auch die Drehrichtung des Fördermotors und die Fördergeschwindigkeit werden vom Fördermaschinisten über einen Stellhebel beeinflusst, mit dem er einen umschaltbaren Regulierwiderstand betätigt.[36]
Fördermaschinen mit Drehstrommotor
[Bearbeiten | Quelltext bearbeiten]Fördermaschinen mit Drehstrommotor werden meistens bei schwach betriebenen Förderungen verwendet.[13] Bei diesen Drehstromantrieben werden in der Regel Schleifringläufermotoren oder Kurzschlußläufermotoren mit stufenweiser Drehzahlsteuerung verwendet.[36] Bei Antrieben mit Schleifringläufer müssen diese eine Einrichtung haben, die den Motorläufer beim Überschreiten automatisch kurzschließt.[19] Die Drehzahlsteuerung erfolgt über Vorwiderstände, zur Bremsung wurden fußpedalgesteuerte Bremsbacken verwendet.[16] Da gewöhnliche Drehstrommotoren in der Regel nicht für eine für den Förderbetrieb erforderliche genügend niedrige Drehzahl gebaut werden, müssen Drehstromfördermaschinen mit einem Vorgelege ausgerüstet werden.[13] Durch das Getriebe wird die Drehzahl auf etwa 150 Umdrehungen pro Minute herabgesetzt.[16] Anstelle der Drehstrommotoren mit nur einer Drehzahl kommen auch polumschaltbare Motoren zum Einsatz.[19] Da diese Antriebe ohne Umformer auskommen, entfallen bei unregelmäßig genutzten Antrieben die hohen Leerlaufverluste.[13] Vereinzelt wurden auch Drehstrom-Kollektormotoren als Antriebsmaschine für Fördermaschinen verwendet.[46]
Moderne Fördermaschinen
[Bearbeiten | Quelltext bearbeiten]Moderne Fördermaschinen werden entweder von schnelllaufenden Drehstrom- oder Gleichstrommotoren mit nachgeschaltetem Getriebe oder langsamlaufenden stromrichtergesteuerten Gleichstrom- oder Synchronmotoren angetrieben. Moderne Drehstromantriebe werden mit Drehstromasynchronmotoren mit Umrichtersteuerung oder Drehstromsynchronmotoren verwendet.[4] Bei den Antrieben mit Drehstromsynchronmotor werden direktumrichtergespeiste Drehstromnmaschinen ab einer Antriebsleistung über 1 Megawatt verwendet.[48] Langsamlaufende Motoren werden direkt mit der Hauptwelle gekoppelt. Bis 2 Megawatt werden schnell- und über 2 Megawatt langsamlaufende Motoren verwendet. Die Drehzahlstellung erfolgt über unterschiedlich geschaltete Stromrichter.[23] Sehr große Vorteile wie z. B. geringere Investitionskosten, platzsparende Bauweise, einfache Inspektionsmöglichkeit und kundenfreundliche Wartung haben Fördermaschinen mit in den Seilträger integriertem Motor.[49]
Bremseinrichtungen
[Bearbeiten | Quelltext bearbeiten]Bei den Bremseinrichtungen für Fördermaschinen unterscheidet man Trommelbremsen[35] und Scheibenbremsen.[4] Bei den Trommelbremsen unterscheidet man Einbackenbremsen, Doppelbackenbremsen und Innenbackenbremsen.[35] Früher wurden auch einfache Konstruktionen als Bremse für Fördermaschinen verwendet.[27] Einfache Bremsen wie z. B. Bandbremsen sind an heutigen Fördermaschinen nicht mehr zulässig.[50]
Hauptsächlich werden Doppelbackenbremsen als Trommelbremsen für Fördermaschinen verwendet. Bei diesen Bremsen erfolgt die Bremskraftübertragung durch ein Bremsgestänge bei radialer Krafteinwirkung. Aufgrund der beidseitig angeordneten Bremsbacken wird eine Biegebeanspruchung der Welle vermieden. Man unterscheidet zwei Bremssysteme: die Fahr- und die Sicherheitsbremse. Bei der Fahrbremse erfolgt das Bremsen durch eine äußere Energiezufuhr, bei der Sicherheitsbremse erfolgt das Bremsen durch eine äußere Energieabfuhr.[35]
Bei der Scheibenbremse erfolgt die Krafterzeugung durch Druckfedern.[4] Durch vorgespannte und hydraulisch gesteuerte Tellerfedern werden die Bremsklötze auf die Bremsscheibe gedrückt.[51] Beim Bremsen erfolgt Druckminderung und damit verbundener Energieabfuhr. Scheibenbremsen haben große Vorteile gegenüber Trommelbremsen. Sie sind thermisch hoch belastbar und die Bremskraft ist auf mehrere Elemente aufgeteilt.[4] Aufgrund des geringeren Platzbedarfes lassen sich mit ihnen besser Mehrseilförderungen erstellen. Mit Scheibenbremsen lässt sich durch das Ansprechen einzelner Bremselemente eine konstante Verzögerung ermöglichen. Außerdem lässt sich eine Bremskrafterhöhung durch den Einbau zusätzlicher Bremselemente leichter realisieren.[51]

Aufstellungsort
[Bearbeiten | Quelltext bearbeiten]Hinsichtlich des Aufstellungsortes der Fördermaschine unterscheidet man Flur- und Turmfördermaschinen.[21] Welche Aufstellungsart bei einer neu zu errichtenden Fördermaschine bevorzugt wird, hängt von den örtlichen Gegebenheiten ab[23] und davon, mit welchem Seilträger die Fördermaschine ausgestattet ist.[21]
Flurförderanlagen
[Bearbeiten | Quelltext bearbeiten]Bei Flurförderanlagen befindet sich die Fördermaschine ebenerdig in einiger Entfernung vom Fördergerüst in einem separaten Fördermaschinengebäude.[23] Hier ist die Fördermaschine annähernd auf Geländehöhe montiert.[5] Zur Umlenkung des Förderseils dienen Seilscheiben im Fördergerüst.[21] Dabei müssen die Lage der Fördermaschine und die Lage der Seilscheiben soweit übereinstimmen, dass sich die Seilscheibenebene mit der Seilträgerebene senkrecht schneidet.[5]
Turmförderanlagen
[Bearbeiten | Quelltext bearbeiten]Bei einer Turmförderanlage befindet sich die gesamte Fördermaschine im Förderturm, senkrecht über der Schachtöffnung.[23] Mittels einer Ablenkscheibe wird die Lage des Förderseils geringfügig korrigiert.[21] Diese Anordnung der Fördermaschine ist sehr platzsparend, da keine weiteren Gebäude auf dem Bergwerksgelände benötigt werden.[52] Allerdings ist bei dieser Art der Aufstellung der Fördermaschine die Seilbelastung deutlich größer, da die dynamischen Kräfte konstruktionsbedingt in kürzere Seilstrecken eingeleitet werden.[23] Außerdem sind aufgrund der größeren Seilablenkung Trommelfördermaschinen nicht als Turmfördermaschinen geeignet.[21]
Betrieb
[Bearbeiten | Quelltext bearbeiten]Der Betrieb der Fördermaschine obliegt dem Fördermaschinisten.[53] Den Stand des Korbes kann der Fördermaschinist anhand des Teufenanzeigers bestimmen.[35] Der exakte Stand wird durch Farbmarkierungen auf dem Seil angegeben. Für die Bedienung der Fördermaschine insbesondere für das genaue Positionieren der Förderkörbe mit verschiedenen Beladungen ist viel Fingerspitzengefühl notwendig. Das Bedienen der Fördermaschine ist insbesondere bei Seilfahrten eine verantwortungsvolle Aufgabe.[15] Die Kommunikation zwischen den Sohlen und dem Fördermaschinisten erfolgt über akustische Signale, die elektrisch übertragen werden.[54] Zur Kommunikation bei Schachtarbeiten dient der sogenannte Schachthammer.[55] Der Anschläger ist eine Person, die auf den vom Korb regelmäßig angefahrenen Sohlen den Betrieb am Schacht überwacht. Der Anschläger kommuniziert mit dem Fördermaschinisten mittels der Signalanlage (Schachthammer, Fertigsignalanlage; früher mechanisch, heute meist elektrisch/elektronisch). An Nebenschächten ohne regelmäßige Seilfahrt können unterwiesene Bergleute das Signal für die Fahrt selbst geben (so genannte Selbstfahrer).[56]
Leistungsdaten
[Bearbeiten | Quelltext bearbeiten]Die wichtigsten Leistungsdaten bei einer Schachtförderanlage sind die Nutzlast, die die Fördermaschine bewegen kann, und die Fördergeschwindigkeit, mit der sie diese Nutzlast bewegen kann.[4]
Die derzeit größte und leistungsstärkste Fördermaschine der Welt befindet sich auf dem Bergwerk South Deep in Südafrika.[23] Es handelt sich um eine Zweiseil-Doppeltrommelfördermaschine der Bauart Blair.[57] Die vier Förderseile sind je 3345 m lang. Die Fördermaschine kann eine Nutzlast von 31 t mit einer maximalen Fördergeschwindigkeit von 18 m/s aus einer Teufe von 3000 m bewegen.[23] Der Elektromotor der Fördermaschine hat eine Antriebsleistung von 12,8 MW.[57][58]
Die leistungsstärkste Treibscheibenfördermaschine ist am Gotthard-Basistunnel in einem Blindschacht installiert.[59] Der Elektromotor hat eine Antriebsleistung von 4,2 MW.[60] Die Fördermaschine kann damit Nutzlasten von 50,8 t mit einer Fördergeschwindigkeit von 18 m/s aus einer Teufe von 800 m bewegen.[59]
Die größte Treibscheibenfördermaschine Deutschlands ist die Achtseilanlage des Schachtes Zielitz I mit 50 t Nutzlast.[58]
Literatur
[Bearbeiten | Quelltext bearbeiten]- Julius, Ritter von Hauer: Die Fördermaschinen der Bergwerke. 2. Auflage. Verlag von Arthur Felix, Leipzig 1874.
Einzelnachweise
[Bearbeiten | Quelltext bearbeiten]- ↑ a b Wilhelm Hermann, Gertrude Hermann: Die alten Zechen an der Ruhr. 4. Auflage. Verlag Karl Robert Langewiesche, Nachfolger Hans Köster KG, Königstein i. Taunus, 1994, ISBN 978-3-7845-6994-9.
- ↑ a b c d e f g h i Hans Bansen (Hrsg.), Fritz Schmidt: Die Bergwerksmaschinen. Eine Sammlung von Handbüchern für Betriebsbeamte. Dritter Band, Die Schachtfördermaschinen. Zweite, vermehrte und verbesserte Auflage, erster Teil; Die Grundlagen des Fördermaschinenwesens, mit 178 Abbildungen im Text, Verlag von Julius Springer, Berlin 1923, S. 1, 2, 6, 9, 10, 16, 17.
- ↑ a b c d e Albert Serlo: Leitfaden der Bergbaukunde. Zweiter Band, dritte verbesserte und bis auf die neueste Zeit ergänzte Auflage, mit 640 in den Text gedruckten Holzschnitten und 23 lithographischen Tafeln, Verlag von Julius Springer, Berlin 1878, S. 97, 98.
- ↑ a b c d e f g h Liu Bin: Schachtförderanlagen deren Auslegung Konstruktion und Sicherheitsnormen. Diplomarbeit am Lehrstuhl für Fördertechnik und Konstruktionslehre der Montanuniversität Leoben, Leoben 2015, S. 4, 25–28.
- ↑ a b c Hans Bansen (Hrsg.), Karl Teiwes, E. Förster: Die Bergwerksmaschinen. Eine Sammlung von Handbüchern für Betriebsbeamte. Dritter Band, Die Schachtfördermaschinen. Verlag von Julius Springer, Berlin 1913, S. 1–10.
- ↑ a b Otfried Wagenbreth, Eberhard Wächter: Der Freiberger Bergbau. Technische Denkmale und Geschichte. Mit 315 Bildern, davon 215 als Fotografien und 28 Tabellen, 2. Auflage, Nachdruck durch Springer Spektrum Verlag, Berlin 2015, S. 34, 36–39.
- ↑ Kammerer-Charlottenburg: Die Technik der Lastenförderung einst und jetzt. Eine Studie über die Entwicklung der Hebemaschinen und ihren Einfluß auf Wirtschaftsleben und Kulturgeschichte, Druck und Verlag von R. Oldenbourg, München und Berlin 1907, S. 29–33.
- ↑ a b c d Friedrich Balck: Wasserkraftmaschinen für den Bergbau im Harz. Frühzeitliche Spuren und deren Deutung am Beispiel der Grube Thurm Rosenhof und ausgewählter Anlagen, Habilitationsschrift an der Fakultät für Bergbau, Hüttenwesen und Maschinenwesen der Technischen Universität Clausthal, Clausthal-Zellerfeld 1999, S. 4, 5, 21–37.
- ↑ a b Heinrich Otto Buja: Ingenieurhandbuch Bergbautechnik, Lagerstätten und Gewinnungstechnik. 1. Auflage, Beuth Verlag GmbH Berlin-Wien-Zürich, Berlin 2013, ISBN 978-3-410-22618-5, S. 6, 7.
- ↑ a b Der Steinkohlenbergbau im Zwickauer Revier. Steinkohlenbergbauverein Zwickau e. V., Förster & Borries, Zwickau 2000, ISBN 3-00-006207-6.
- ↑ a b Kurt Pfläging: Die Wiege des Ruhrkohlenbergbaus. Die Geschichte der Zechen im südlichen Ruhrgebiet. 4. Auflage. Verlag Glückauf, Essen 1987, ISBN 3-7739-0490-8, S. 93, 138.
- ↑ a b F. Niethammer (Hrsg.): Generatoren, Motoren und Steuerapparate für elektrisch betriebene Hebe- und Transportmaschinen. Mit 805 in den Text gedruckten Abbildungen, R. Oldenbourg Verlag, München 1900, S. 302–308.
- ↑ a b c d e f g Carl Hellmut Fritzsche: Lehrbuch der Bergbaukunde. Erster Band, neunte völlig neubearbeitete Auflage, mit 584 Abbildungen und einer farbigen Tafel, Springer Verlag, Berlin/Göttingen/Heidelberg 1955, S. 473–477.
- ↑ a b c d Karl Heinz Bader, Karl Röttger, Manfred Prante: 250 Jahre märkischer Steinkohlenbergbau. Ein Beitrag zur Geschichte des Bergbaues, der Bergverwaltung und der Stadt Bochum. Studienverlag Dr. N. Brockmeyer, Bochum 1987, ISBN 3-88339-590-0, S. 54, 95.
- ↑ a b F. Mechtold: Hebe- und Förderanlagen; Grundlagen - Bauarten - Anwendungen. 5. völlig neubearbeitete und stark erweiterte Auflage, Springer Verlag Berlin-Heidelberg-New York, Berlin 1969, S. 488–495.
- ↑ a b c d e f g h i Harald Schmidtbauer: Die frühe technische Nutzung der Elektrizität im Bergbau und Hüttenwesen sowie in der Metallverarbeitung. Beispiele aus dem deutschsprachigen Raum bis zum Ersten Weltkrieg. Diplomarbeit an der Universität Wien, Wien 2013, S. 34, 40–48.
- ↑ a b c d e Hartmut Arnold: Überblick über den heutigen Stand der Schachtförderung in der Bundesrepublik Deutschland unter besonderer Berücksichtigung der Verhältnisse im Steinkohlenbergbau. In: Kommission der Europäischen Gemeinschaften (Hrsg.). Fördertechnik im Steinkohlenbergbau unter Tage. Informationstagung in Luxemburg vom 24. bis 26. März 1978, Band 1, Verlag Glückauf GmbH, Gedruckt in Belgien 1979, ISBN 3-7739-0233-6, S. 343, 346, 347.
- ↑ C. Klinger, M. Eckart, P. Rüterkamp, T. Steinmetz: Einfluss eines Wasseranstiegs durch Einstellung der Wasserhaltungen Zollverein, Carolinenglück, Amalie und AV auf die PCB- und sonstigen Stoffgehalte im Grubenwasser. DMT Abschlussbericht, DMT-Bearbeitungs-Nr. FEE4-2018-02359, Essen 2019, S. 19.
- ↑ a b c d Technische Anforderungen an Schacht- und Schrägförderanlagen (TAS). Verlag Hermann Bellmann, Dortmund 2005, Blatt 3/1 - Blatt 3/3.
- ↑ Heinz Pfeifer, Gerald Kabisch, Hans Lautner: Fördertechnik. Konstruktion und Berechnung, 6. Auflage, Springer Fachmedien, Wiesbaden 1995, ISBN 978-3-528-54061-6, S. 10–22.
- ↑ a b c d e f Horst Roschlau, Wolfram Heintze: Bergmaschinentechnik. Erzbergbau, Kalibergbau. VEB Deutscher Verlag für Grundstoffindustrie, mit 333 Bildern und 54 Tabellen, Leipzig 1977, S. 256–260.
- ↑ a b Walter Bischoff, Heinz Bramann, Westfälische Berggewerkschaftskasse Bochum: Das kleine Bergbaulexikon. 7. Auflage. Verlag Glückauf GmbH, Essen 1988, ISBN 3-7739-0501-7.
- ↑ a b c d e f g h i W. Sindern, St. Borowski: Sicherheitstechnische Betrachtungen zu Schachtförderanlagen für den Zugang zu einem zukünftigen geologischen Tiefenlager. Arbeitsbericht NAB 14-75, Nationale Genossenschaft für die Lagerung radioaktiver Abfälle (Hrsg.), Wettingen 2014, S. 29, 39, 41.
- ↑ Horst Roschlau, Wolfram Heinze, SDAG Wismut (Hrsg.): Wissensspeicher Bergbautechnologie. 1. Auflage. Deutscher Verlag für Grundstoffindustrie, Leipzig 1974, S. 183–186.
- ↑ Tilo Cramm, Joachim Huske: Bergmannssprache im Ruhrrevier. 5. überarbeitete und neu gestaltete Auflage, Regio-Verlag, Werne 2002, ISBN 3-929158-14-0.
- ↑ a b Hans Bansen (Hrsg.): Die Bergwerksmaschinen. Eine Sammlung von Handbüchern für Betriebsbeamte. Vierter Band, Die Schachtförderung. Verlag von Julius Springer, Berlin 1913, S. 3.
- ↑ a b c d Friedrich Balck: Vom Wasserrad zum elektrischen Antrieb. Entwicklung der Fördermaschinen im Rosenhöfer Revier bei Clausthal, Schriftenreihe des Oberharzer Geschichts- und Museumsvereins e. V. Clausthal-Zellerfeld, 1. Auflage, Clausthal-Zellerfeld 1999, ISBN 3-9806619-0-3, S. 41, 48, 53, 54, 57–37.
- ↑ Jens Pfeifer: Die Fahrkünste im Freiberger Revier mit besonderer Berücksichtigung des Fahrkunstunglücks vom 29. Februar 1880 auf dem Abrahamschacht der Himmelfahrt Fundgrube. In: Wolfgang Ingenhaeff, Johann Bair (Hrsg.). Bergbau und Kunst. Band III Technische Künste (Wasserkunst, Wetterkunst, Markscheidekunst, Förderkunst, Fahrkunst, Schmelzkunst etc.), Tagungsband 11. Montanhistorischer Kongress Schwaz, Berenkamp Verlag, Wattens 2013, S. 212, 213.
- ↑ Emil Stöhr, Emil Treptow: Grundzüge der Bergbaukunde einschließlich der Aufbereitung. Spielhagen & Schurich Verlagsbuchhandlung, Wien 1892.
- ↑ a b Sven Bardua, Norbert Gilson: Die Dampfkraft Inbegriff des Industriezeitalters. In: Landschaftsverband Rheinland, Landschaftsverband Westfalen, u. a. (Hrsg.). Industriekultur. Denkmalpflege, Landschaft, Sozial-, Umwelt und Technikgeschichte; 21. Jahrgang, Heft 73, Ausgabe 4 / 2015, Klartext Verlag, Essen 2015, S. 2–4.
- ↑ Alfred Nehls: Aller Reichtum lag in der Erde. Die Geschichte des Bergbaus im Oberbergischen Kreis, Verlag Gronenberg, Gummersbach 1993, ISBN 3-88265-180-6, S. 41.
- ↑ a b c Herbert Pforr: Das erzgebirgische Kunstgrabensystem und die Wasserkraftmaschinen für Wasserhaltung und Schachtförderung im historischen Freiberger Silberbergbau. In: Ring Deutscher Bergingenieure e. V. (Hrsg.): Bergbau. Makossa Druck und Medien GmbH, Gelsenkirchen 2007, S. 502–505 Online ( vom 4. Oktober 2013 im Internet Archive) (zuletzt abgerufen am 30. Oktober 2012; PDF-Datei; 646 kB).
- ↑ a b Philipp Lechner: Die Dampfmaschine von James Watt – physikalische Prinzipien, technische Umsetzungen, gesellschaftliche Auswirkungen. Diplomarbeit am Institut für Theoretische Physik der Johannes Keppler Universität Linz, Linz 2015, S. 60–72.
- ↑ Amadee Burat, Carl Hartmann: Das Material des Steinkohlenbergbaues. Verlag von August Schnee, Brüssel/Leipzig 1861.
- ↑ a b c d e f g H. Hoffmann: Lehrbuch der Bergwerksmaschinen (Kraft und Arbeitsmaschinen). Mit 523 Textabbildungen. Springer Verlag GmbH, Berlin 1926, S. 188–199.
- ↑ a b c d e f g h H. Hoffmann, C. Hoffmann: Lehrbuch der Bergwerksmaschinen (Kraft und Arbeitsmaschinen). Mit 587 Textabbildungen, 3. Auflage, Springer Verlag OHG, Berlin 1941, S. 45–52, 262-269.
- ↑ O. Rosahl: Belastungsstöße und Speicherfähigkeit in Dampfkraftbetrieben. Vulkan – Verlad Dr. W. Classen, Essen 1942, S. 28–31.
- ↑ Verein für bergbauliche Interessen im Oberbergamtsbezirk Dortmund (Hrsg.): Die Entwicklung des Niederrheinisch-Westfälischen Steinkohlen-Bergbaues in der zweiten Hälfte des 19. Jahrhunderts. Teil VIII Disposition der Tagesanlagen - Dampferzeugung - Centralkondensation - Luftkompression - Elektrische Centralen, Springer-Verlag Berlin Heidelberg GmbH, Berlin Heidelberg 1905, S. 95–101.
- ↑ Hans Väth: Zechenbauten Über Tage. Dissertation an der Technischen Hochschule Carolo-Wilhelmina, Druck von Fr. Wilh. Ruhfus, Dortmund 1929, S. 16, 32.
- ↑ Freundeskreis Geologie und Bergbau e. V. Hohenstein-Ernstthal ( vom 4. Oktober 2013 im Internet Archive) (zuletzt abgerufen am 30. Oktober 2012).
- ↑ Dampffördermaschinen auf Fürst Leopold ( vom 19. Juni 2012 im Internet Archive) (zuletzt abgerufen am 30. Oktober 2012).
- ↑ Zeche Consolidation Schacht 9 in Gelsenkirchen (abgerufen per Webarchive am 9. Dezember 2021).
- ↑ Gesamtverband Steinkohle e. V.: Vor Ort. Steinkohlenbergbau, Druck B.o.s.s Druck und Medien GmbH, Goch, S. 30.
- ↑ a b Die Entwicklung des elektrischen Fördermaschinen-Antriebs. In: Schweizerische Bauzeitung. Band 73/74, Zürich 1919, S. 95–98.
- ↑ a b c Wilhelm Brüsch: Leitfaden der Elektrizität im Bergbau. Mit 411 Abbildungen im Text, Druck und Verlag von B. G. Teubner, Leipzig 1901, S. 134–139, 209.
- ↑ a b Berg. Ref. Masling: Neuere Arten elektrischer Fördermaschinen mit Drehstromantrieb. In: Glückauf, Berg- und Hüttenmännische Zeitschrift. Verein für die bergbaulichen Interessen im Oberbergamtsbezirk Dortmund (Hrsg.), Nr. 49, 48. Jahrgang, 10. 7. Dezember 1912, S. 1981–1991.
- ↑ A. Senner: Fachkunde Elektrotechnik. 4. Auflage, Europa-Lehrmittel Verlag, 1965, S. 218, 233.
- ↑ Wolfgang Schubert: Aus der Tiefe - der Steinkohlenbergbau in Deutschland. In: Gesamtverband Steinkohle e. V. (Hrsg.). Mining Report Glückauf 154. No. 6, Bergbau Verlagsgesellschaft mbH, Essen 2018, ISSN 2195-6529, S. 491.
- ↑ Matthias Bohn, Detlef Scheppe, Klaus Hofmann: Die weltweit höchste Einzelförderschachtleistungen durch SIEMAC TECBERG Fördermaschinen mit integriertem Antrieb. In: Oliver Langenfeld (Hrsg.): Kolloquium Fördertechnik im Bergbau 2016. 1. Auflage, Papierfliegerverlag, Clausthal-Zellerfeld 2016, ISBN 978-3-86948-481-5, S. 197, 198.
- ↑ Fachbereichsstandard Bergbau unter Tage Schachtförderanalgen. Technische Forderungen an Fördermaschinen und Schachtwinden. TLG 39641/03, Gruppe 131267, Verlag für Standardisierung, Leipzig 1983, Lizenz Nr. 785 – 357/83 ST 997, S. 3–9.
- ↑ a b Technische Information Scheibenbremsen für Fördermaschinen. Siemag Tecberg (abgerufen am 10. September 2012; PDF-Datei; 581 kB)
- ↑ Steinkohlenportal Artikel: Tempo im Schacht ( vom 26. Juni 2009 im Internet Archive) (abgerufen am 30. Oktober 2012).
- ↑ O. Leidenroth: Die psychotechnische Eignungsprüfung von Fördermaschinisten. In: Glückauf, Berg- und Hüttenmännische Zeitschrift. Verein für die bergbaulichen Interessen im Oberbergamtsbezirk Dortmund (Hrsg.), Nr. 49, 64. Jahrgang, 10. 8. Dezember 1928, S. 1648–1651.
- ↑ Thüringer Bergverordnung für Schacht- und Schrägförderanlagen (ThürBVOS) vom 1. November 2004.
- ↑ Verein für Bergbau und Sozialgeschichte Dorsten: Der Fördermaschinist ( vom 6. Oktober 2013 im Internet Archive) (zuletzt abgerufen am 30. Oktober 2012)
- ↑ Bergverordnung für Schacht- und Schrägförderanlagen (BVOS) § 24 Selbstfahrerseilfahrt (abgerufen am 30. Oktober 2012).
- ↑ a b Siemag Tecberg: Trommel-Fördermaschinen Beispiele ( vom 14. August 2010 im Internet Archive) (abgerufen am 30. Oktober 2012).
- ↑ a b Winfried Sindern, Olivier Gronau: Stahldrahtseile – bewährte Leistungsträger von Schachtförderanlagen. In: Ring Deutscher Bergingenieure e. V. (Hrsg.): Bergbau. 61. Jahrgang, Nr. 4. Makossa Druck und Medien GmbH, April 2010, ISSN 0342-5681, S. 155–164.
- ↑ a b Michael Flender: Gotthard-Basistunnel: Die Schachtförderanlage von Sedrun. Teil 1 Rohbauphase. In: GeoRessources Portal Manfred König (Hrsg.): GeoRessources Journal, Fachzeitschrift für den Bergbau, 1. Jahrgang 2015, Duisburg 2015, ISSN 2364-0278, S. 28–30.
- ↑ Siemac Tecberg Koepe-Fördermaschinen Beispiele ( vom 14. August 2010 im Internet Archive) (abgerufen am 30. Oktober 2012)
Weblinks
[Bearbeiten | Quelltext bearbeiten]- Koepe-Fördermaschine mit Elektromotor (abgerufen am 30. Oktober 2012)
- Beispiele von Fördermaschinen (abgerufen am 10. Juni 2016)
Anmerkungen
[Bearbeiten | Quelltext bearbeiten]- ↑ Die Größe der Kehrräder richtete sich nach der Fallhöhe und der verfügbaren Menge an Aufschlagwasser sowie der benötigten Antriebsleistung. (Quelle: Heinrich Otto Buja: Ingenieurhandbuch Bergbautechnik, Lagerstätten und Gewinnungstechnik.)
- ↑ Diese umfangreichen maschinellen Anlagen (Umformer + Fördermaschine) hatten gegenüber der Dampfmaschine einen hohen Anschaffungspreis, was häufig dazu führte, dass Dampffördermaschinen bevorzugt wurden und es noch mehrere Jahre dauerte bis sich die elektrischen Fördermaschinen durchsetzen konnten. (Quelle: Berg. Ref. Masling: Neuere Arten elektrischer Fördermaschinen mit Drehstromantrieb.)